Robot Integration
Managing the complexities of robotics system development ensuring compatibility, interoperability and faster deployment.
Robots can bring a huge advantage for companies in every sector, but the complexity associated with introducing and managing industrial robots remains a challenge. Choosing the right tool to integrate all kinds robots and the current systems is crucial to its successful deployment. This process requires expertise in specific robot programming tools and engineering software that isn’t always available within the company. It can be a time-consuming and costly exercise to obtain this knowledge from external experts, that is why Parmley Graham is here to help you manage these complexities.
To find out more about our Robotics Solutions or to discuss your requirements, please contact us to speak with our experts.
Overview
Robot Integration - time to move to a one-system approach
Since robotic automation is often a significant investment, you must ensure your equipment can handle the unique needs of your facility’s application. Unfortunately, most robot manufacturers lack the resources to customise robots to fit the needs of every end-user – leading to issues when it comes to the aspect of robot integration.
Increasing digitalisation requires robot integration
With solutions for robot integration – turn challenges into success!
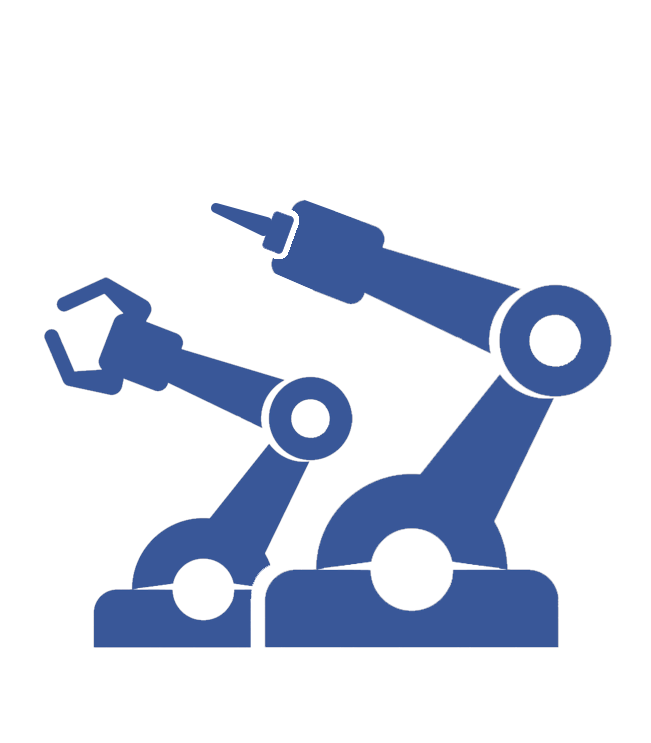
Use robots from different vendors
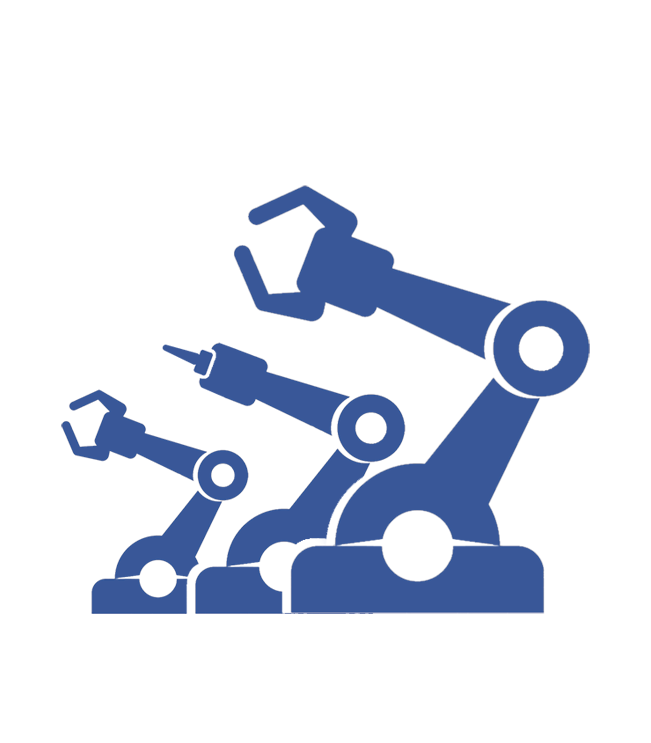
Reduce complexity of introducing robots
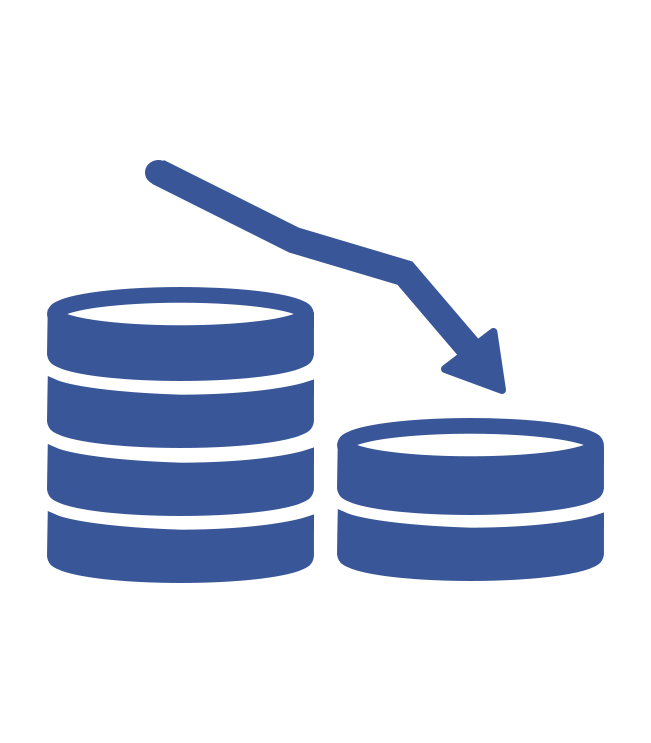
Reduce project and manufacturing costs
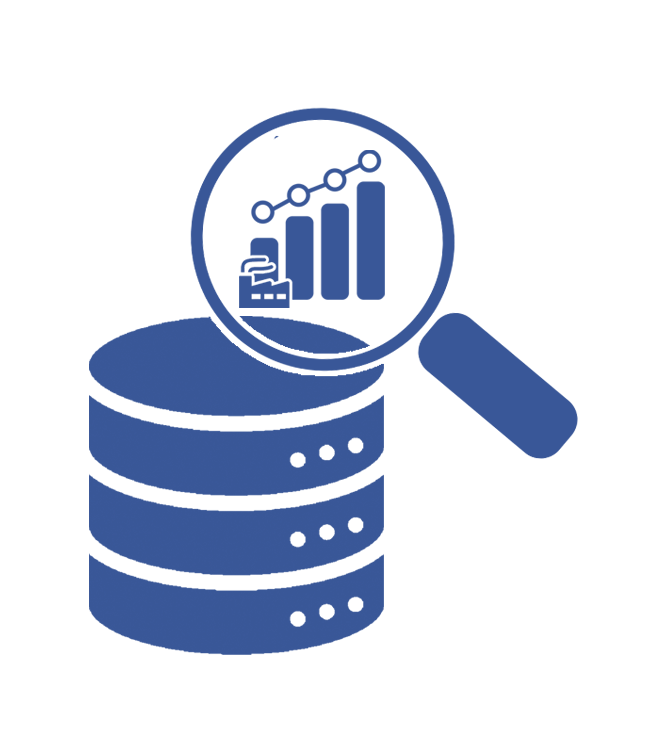
Achieve data transparency
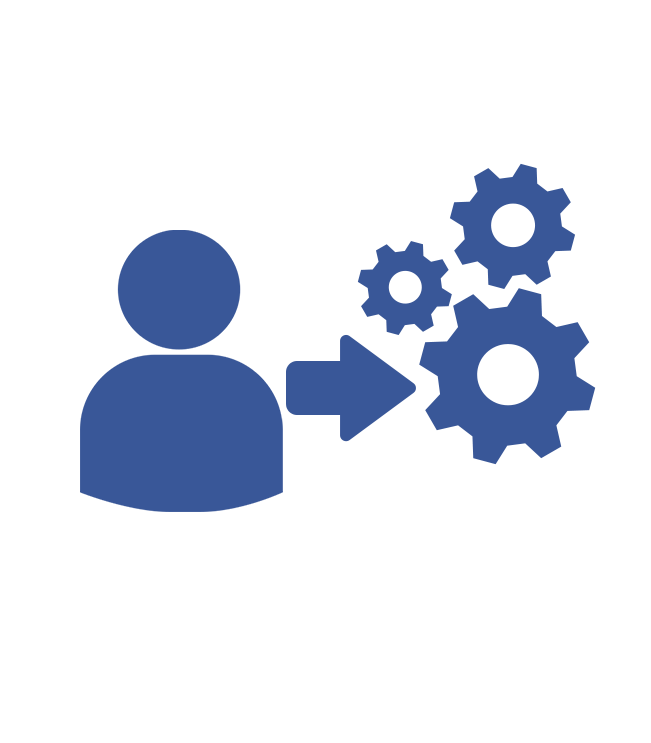
Easy to implement
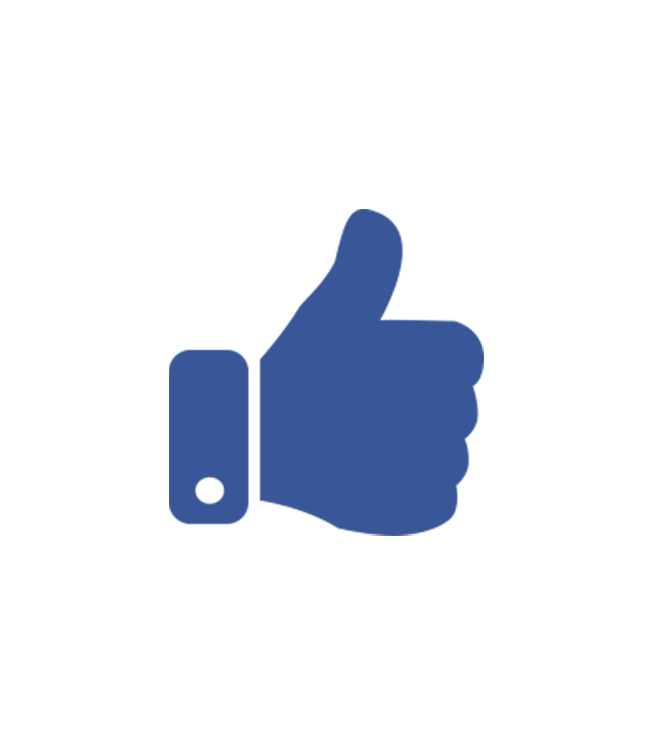
Easy to use
Understanding and overcoming technological, organisational and operational challenges.
Identify requirements
Before integrating robots with other systems, having a clear understanding of what you want to achieve, what resources you have, and what constraints you face, is paramount
Define your functional, performance, safety, and reliability requirements, as well as your budget, timeline, and scope.
It’s ideal also to identify the stakeholders, users, and customers involved in the project and to gain their expectations and feedback.
Choose compatible systems
One of the main challenges of integrating robots with other systems is ensuring compatibility and interoperability. Choose systems that have compatible hardware, software, and communication interfaces as well as consider the standards, protocols, and formats that the systems use and how they can exchange data and commands. Avoid using proprietary or outdated systems that may limit your options or cause compatibility issues.
Test and Debug
Another challenge of integrating robots with other systems is testing and debugging. You should test each system individually and then as a whole to ensure that they work as expected and meet your requirements. You should use simulators, emulators, or mock-ups to test the systems in a controlled environment before deploying them in the real world. You should also use tools such as logs, monitors, debuggers, or analysers to identify and fix any errors, bugs, or glitches that may occur during the integration process.
Adapt to the environment
Consider the physical, social, and ethical aspects of the environment where the robots will operate and how they may affect the integration.
Account for factors such as noise, light, temperature, humidity, obstacles, interference, or human interaction that may influence the performance or behaviour of the systems.
Comply with the laws, regulations, and norms that govern the use of robots in the environment and respect the rights, privacy, and dignity of the people involved.
You need the right tool to integrate all kinds of robots!
The right tool can act as an interface between your robots and systems. It can help reduce the complexity associated with introducing and managing industrial robots and act as an interface between the robots and the current systems.
To take advantage of robotic integration, it used to be that you required the services of third-party robotic integrators who would evaluate each project to determine the best robotic technology for the job – that process is changing and our partner Siemens has the solution to make robot integration easy!
SIMATIC Robot Integrator
One application for robots from different manufacturers
Robot Integration made easy
The SIMATIC Robot Integrator from our partner Siemens now makes the benefits of robotics readily available to all users. Achieve more while reducing the amount of engineering and operational complexity. SIMATIC Robot Integrator is a ready-to-use solution that enables the integration of robots from a wide range of manufacturers without external assistance!
To integrate robots, you just need to know your way around the TIA Portal. That helps to save on engineering costs and users benefit from a single engineering environment for machines and robots.
With solutions for Robot Integration – turn challenges into success!
Find out more about the SIMATIC Robot Integrator.
"Thanks to the app, we achieved a 30% time-saving in the programming of the first bundle of bottles."
Key Advantages
Reap the benefits of robots in a quick and easy process.
Achieve more with less time and effort – the SIMATIC Robot Integrator is a ready-to-use solution that offers extensive benefits to machine builders and end customers.
Benefits in Engineering
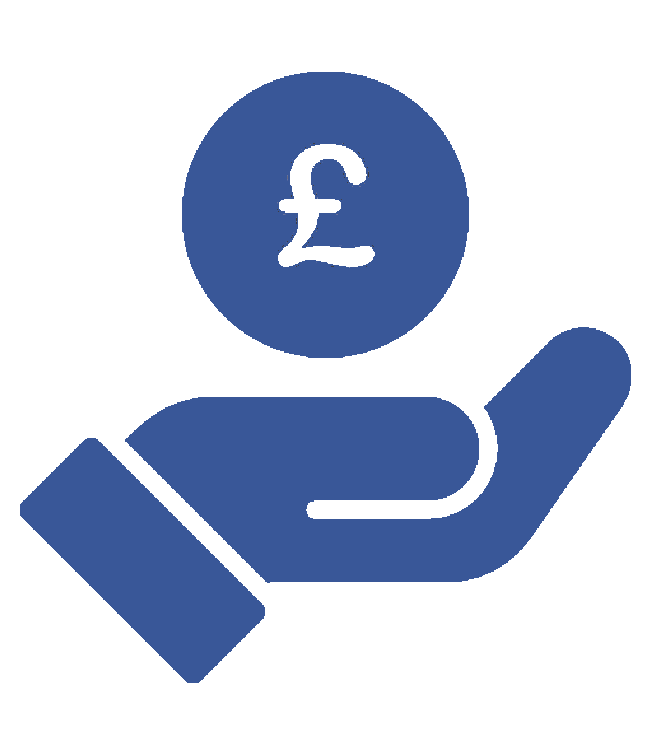
Reduce Expenses
Benefit from a single engineering environment and critically reduce the time and money spent on engineering.
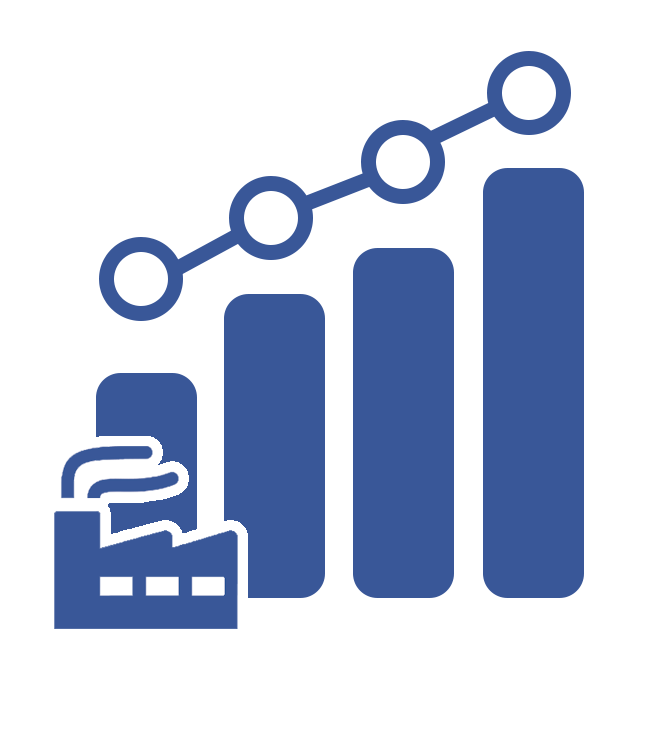
Increase Efficiency
Increase efficiency thanks to a uniform operating concept for PLCs and robots, multivendor robot programming, and uniform HMI faceplates for robots from different manufacturers.
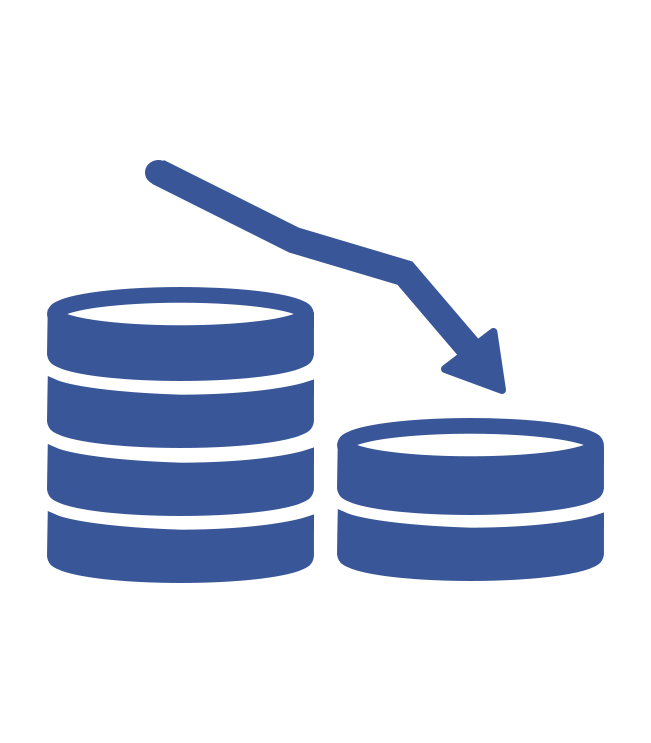
Reduce Error Cost
Reduce programming errors because you can simply adopt the programs thanks to manufacturer-independent robot programming.
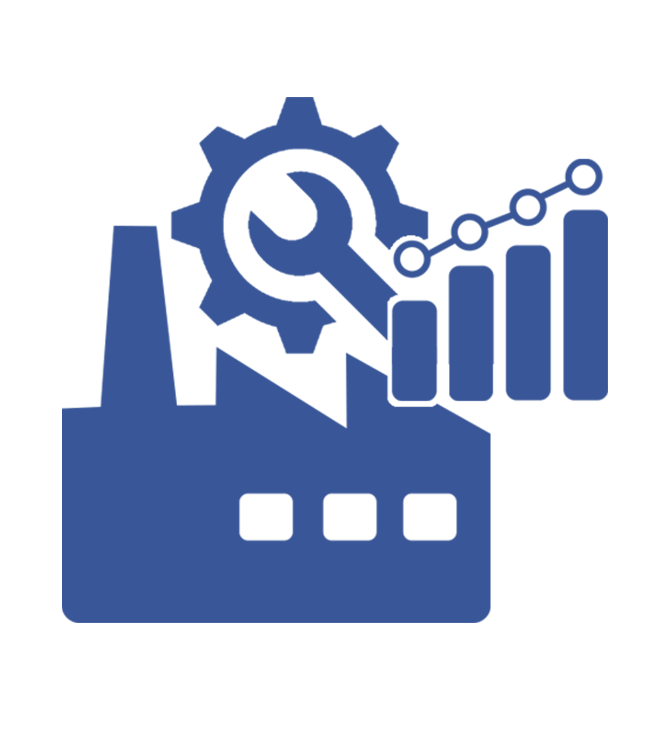
Optimise Maintenance & Diagnostics
Simplify motion control task engineering thanks to integrated technology objects and an intuitive operation with guided user interfaces (GUI).
Benefits in Operation
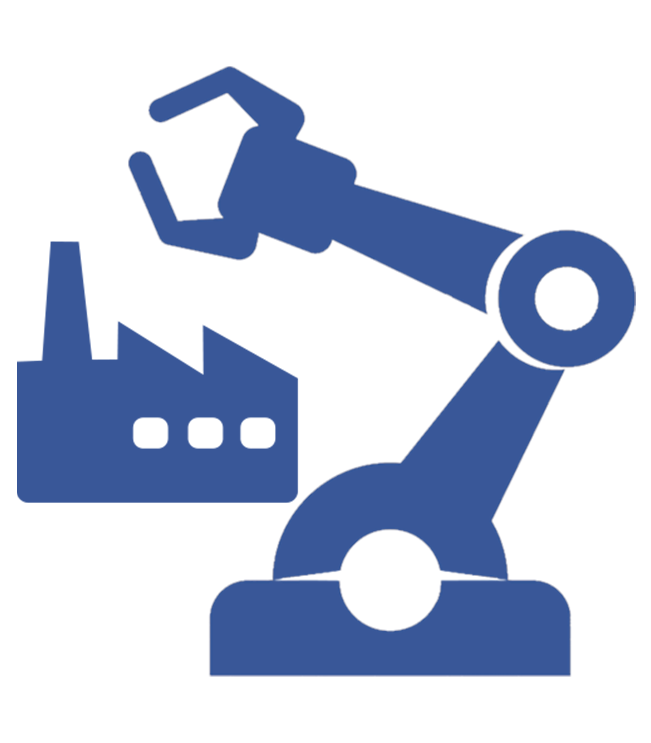
Facilitate Operation
Operate your robot functions when you need to, without external assistance.
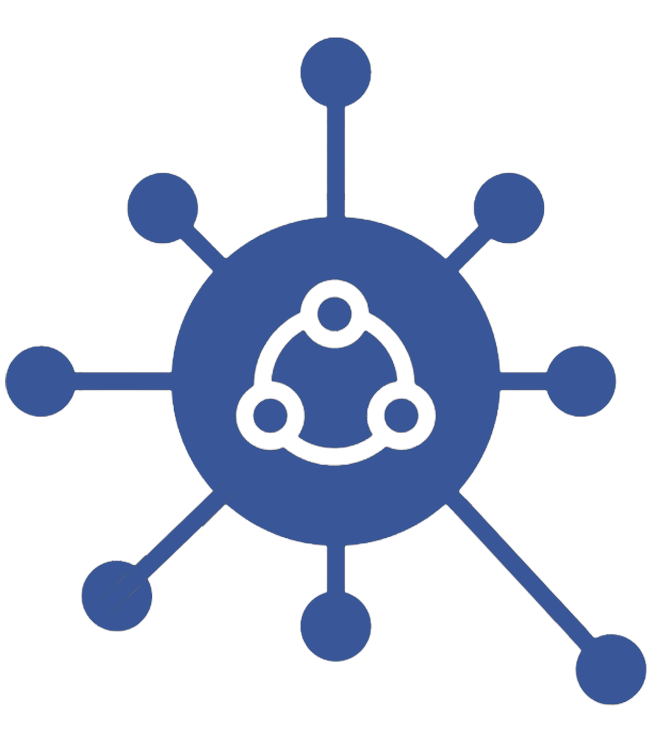
Reduce Complexity
Simplify implementation of standardisation, servicing, and maintenance strategies.
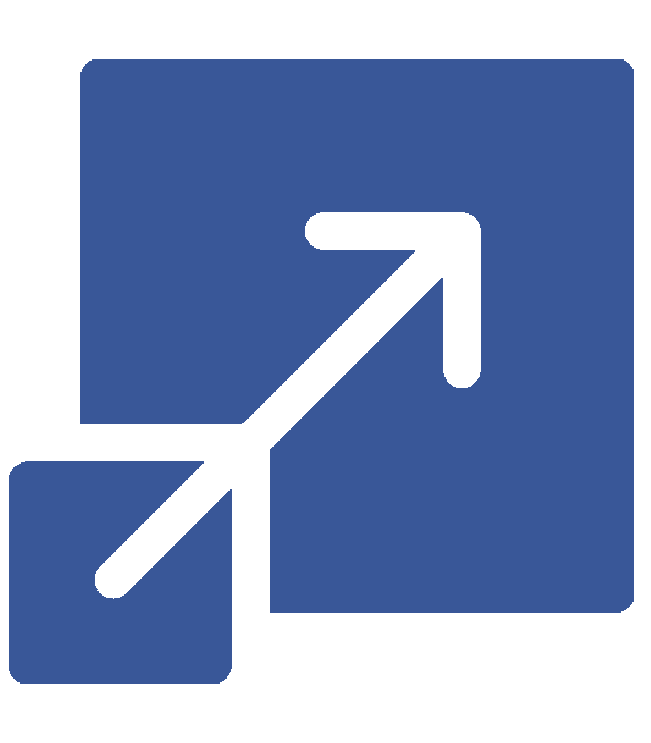
Increased Flexibility
Benefit from TIA diagnostic capabilities all the way to the robot cell.
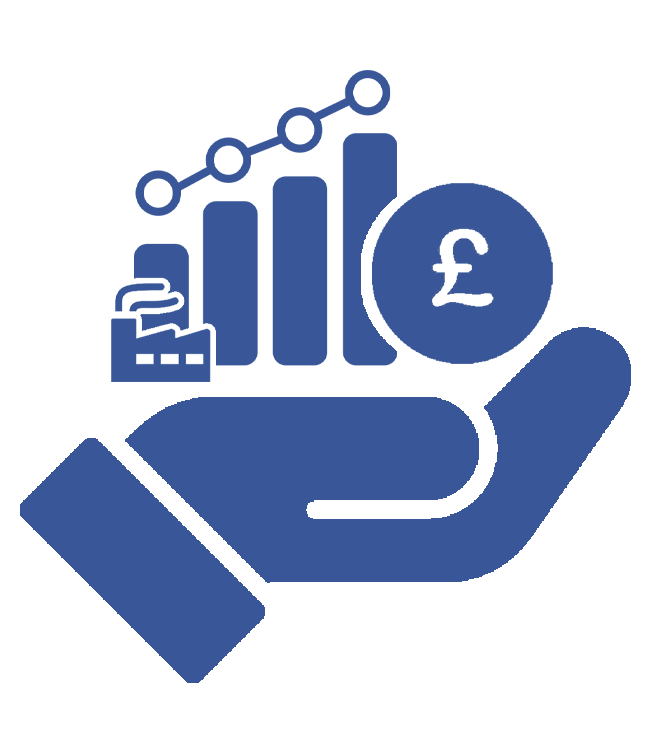
Boost Business
Expand your range of products and services by developing new business models through the use of robots.
For your specific requirements, talk to us.
To see how we can help with your systems or if you have any enquiry, please get in touch – we’ll be pleased to help. Send us an email at support@parmley-graham.co.uk or fill the form below.
Robot Partnerships enable efficiencies for our customers.

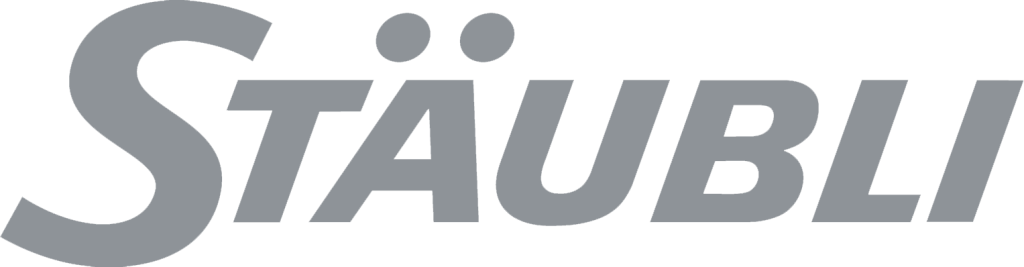
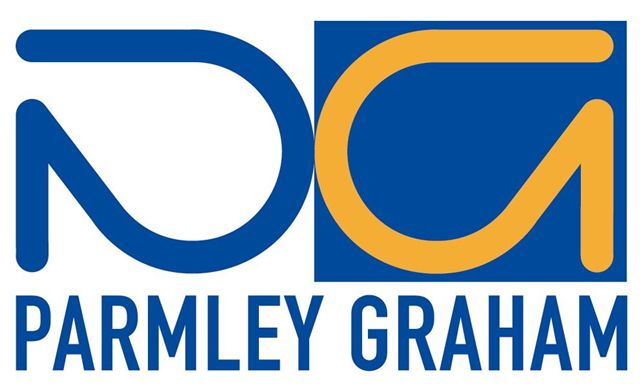
Parmley Graham is a distributor for two of the leading international players in robotics, namely Stäubli Robotics and KUKA.
With Robot Integrator able to integrate with robots from Stäubli, it enables us to offer efficiency in your process and means that its robots can now be easily programmed and run using software and systems from Siemens.
Stäubli estimates time savings of up to 30% for programming and integration thanks to the universal language and reusable programming codes!
With KUKA, typically the plant control system and the robot controller are two different systems; communication between the two controllers takes place mostly only at the bit level and the robot’s motion programs are permanently stored on the robot controller and can only be called by the plant control system. Therefore, it is relatively difficult to implement a flexible response of the robot to special plant events.
Furthermore, the programming of the plant control system and the robot mostly differ to a great extent so that both systems can generally not be supported by one person. Interface and coordination problems are therefore inevitable.
KUKA can use the SIMATIC S7-1500 controller from Siemens to fully control and cooperate with its robots. Communication between the S7-1500 controller and the KUKA industrial robot takes place via a PROFINET connection. All commands and status information between the SIMATIC controller and the robot are exchanged via this connection.
Find out more about KUKA
Find out more about Stäubli
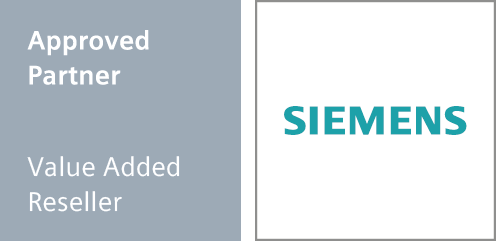
We are Siemens trusted and approved distribution partner.
As a Value Added Reseller in Siemens’ Approved Partner network, Parmley Graham are a proven supplier of a wide range of quality products in the UK and globally.
Find out more how this will benefit you or check Siemens Configurator.