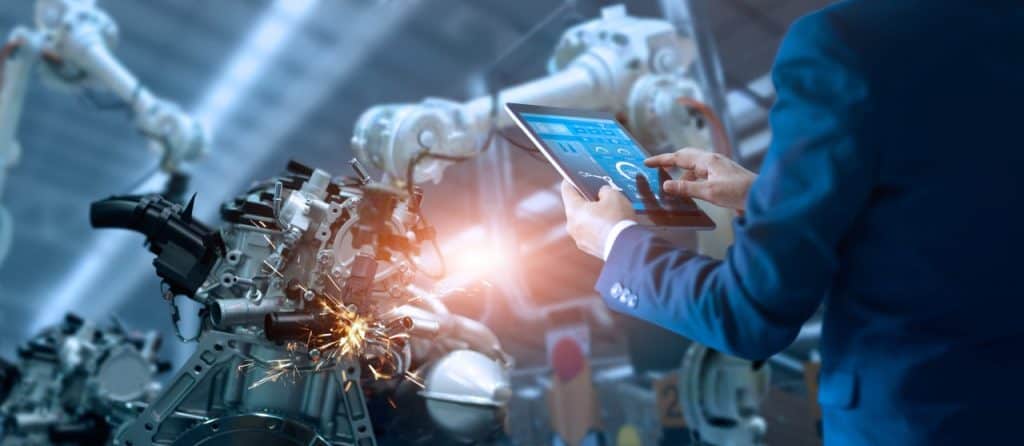
Source: https://www.automationmagazine.co.uk/
Industry 4.0 and the Industrial Internet of Things (IIoT) are interrelated concepts driving modern manufacturing. Industry 4.0 represents the fourth industrial revolution, focusing on automation, data exchange, and integration of smart technology. IoT extends this by connecting machines, sensors, and devices to enable data collection, analysis, and decision-making in real time.
To better understand the differences between Industry 4.0 and the Industrial Internet of Things, read more:
What is Industry 4.0?
Also called the Fourth Industrial Revolution, Industry 4.0 refers to integrating advanced digital technologies into manufacturing and industrial processes to create smart factories and supply chains. From mobile phones to cars and appliances, these things operate through interconnected machines, robots, and systems that communicate and make decisions autonomously.
At its core, Industry 4.0 harnesses technologies like artificial intelligence (AI), the Internet of Things (IoT), big data analytics, and automation to revolutionise a product’s design, production, and delivery. For instance, sensors embedded in machines collect data, which is then analysed to optimise production schedules, predict maintenance needs, and reduce downtime.
Such transformation enables factories to become more efficient, agile, and responsive to customer demands. Customisation becomes easier as production lines adapt quickly to changing requirements. Additionally, remote monitoring and control allow managers to oversee operations from anywhere, enhancing flexibility and scalability.
Industry 4.0 empowers people with technology to make better decisions and drive innovation. Workers collaborate with intelligent systems, focusing on tasks that require human creativity, problem-solving, and critical thinking. It represents a new age where connectivity, data, and automation converge to create more sustainable and competitive industries.
What is Industrial Internet of Things?
The Industrial Internet of Things (IIoT) refers to the network of interconnected devices, sensors, machines, and systems in industrial settings, enabling data collection, analysis, and automation to optimise processes and enhance productivity.
Imagine a factory where every machine, conveyor belt, and assembly line has sensors that collect data on temperature, pressure, speed, and other variables. These sensors transmit information to a central system via the internet, where it’s analysed in real-time to monitor performance, identify inefficiencies, and predict maintenance needs.
IIoT enables factories to become more advanced and efficient. For instance, predictive maintenance algorithms can anticipate equipment failures before they occur, minimising downtime and reducing maintenance costs. Similarly, inventory management systems can automatically reorder supplies when stock levels are low, ensuring uninterrupted production.
IIoT extends to various industries aside from factories, such as agriculture and healthcare. In agriculture, sensors monitor soil moisture levels and weather conditions, allowing farmers to optimise irrigation schedules and maximise yields. In healthcare, wearable devices track patients’ vital signs and medication adherence, enabling remote monitoring and personalised care.
IIoT revolutionises how industries operate by harnessing the power of data and connectivity to improve efficiency, reliability, and decision-making, paving the way for more interconnected systems that drive innovation, sustainability, and competitiveness in the digital age.
The Technologies of Industry 4.0
Industry 4.0 has sparked the creation of various new technologies, including Additive Manufacturing, commonly known as 3D printing. This innovation involves building three-dimensional objects layer by layer using a specialised printer. Rather than carving or moulding materials, 3D printing uses plastic, metal, or even food in precise layers to form the final product.
Augmented Reality (AR), a technology born out of Industry 4.0, enhances our perception of reality by blending digital information with our physical environment. In Industry 4.0, AR supplements images and videos with extra details provided by computers, which could mean adding labels, instructions, or virtual objects to what we see in real life.
Another technology is the Autonomous Robots, also known as Autobots. These smart machines can carry out tasks independently without constant human oversight. You’ve likely seen them as robotic vacuums or even autonomous helicopters. In places like warehouses and factories, they play a crucial role.
How Does IoT Work?
The Internet of Things (IoT) connects everyday objects to the Internet, enabling them to send and receive data. It embeds sensors, actuators, and connectivity into physical devices, allowing them to collect and exchange information. For instance, a smart thermostat in your home can monitor temperature and adjust settings based on your preferences through a smartphone app.
IoT differs from Industry 4.0 in focus and application. While IoT connects devices for various purposes like home automation or healthcare monitoring, Industry 4.0 specifically targets manufacturing and industrial processes. Industry 4.0 integrates IoT devices with advanced technologies like artificial intelligence, big data analytics, and automation to create smart factories and supply chains.
In Industry 4.0, IoT devices in factories collect real-time data on equipment performance, inventory levels, and production processes. This data is then analysed to optimise operations, predict maintenance needs, and improve efficiency.
In conclusion, IoT is the foundation of Industry 4.0, enabling the connectivity and data exchange necessary for smart manufacturing and industrial automation.
The Challenges of IoT
While the Internet of Things (IoT) offers immense potential for connectivity and automation, it also presents several challenges that companies must address before implementation and to achieve success. One of the biggest challenges has to do with security. IoT devices are vulnerable to cyberattacks, posing risks to privacy, data integrity, and system reliability. Weak authentication mechanisms, unencrypted data transmission, and outdated firmware make IoT ecosystems susceptible to hacking, malware, and unauthorised access.
Another challenge is Data Privacy and Compliance. IoT devices collect vast amounts of sensitive data about individuals, environments, and processes. Data privacy, consent management, and compliance with regulations like GDPR (General Data Protection Regulation) require robust data governance frameworks and security measures.
It can be challenging to manage large-scale IoT deployments due to thousands or millions of connected devices, which can pose significant scalability and complexity challenges. Issues such as network congestion, data overload, and resource constraints demand efficient management, monitoring, and optimisation of IoT infrastructure.
The diversity of IoT devices from different manufacturers may also lead to compatibility and interoperability challenges. Incompatibilities between devices and communication protocols hinder seamless integration and data exchange, limiting the scalability and efficiency of IoT solutions.
In the realm of IoT challenges, hiring a dedicated IoT specialist is essential for companies tackling challenges in security, data privacy, scalability, and compatibility within their IoT ecosystems. Their knowledge guarantees that the operational environment is secure, efficient, and compliant, allowing IoT to reach its full potential.
Discuss Further
If you wish to explore further how Parmley Graham can help with your automation needs, complete your details and we’ll be in touch:
Parmley Graham Industry 4.0 Centre
Introducing the Parmley Graham Industry 4.0 Centre! This technology hub in our Gateshead office is used to present some of the latest developments in factory automation and Industry 4.0 technology, which can be accessed from anywhere in the world.
Book a tour to our Industry 4.0 Centre or arrange a remote meeting.
Book a tour now:
For more information, visit: