S7-1500 Advanced Controllers
SIMATIC S7-1500 controller gives you top performance and built-in viability into the future. You can turn the most sophisticated machine designs into reality thanks to the modular structure of the controller, which provides reliable assistance as you work your way through the digital transformation.
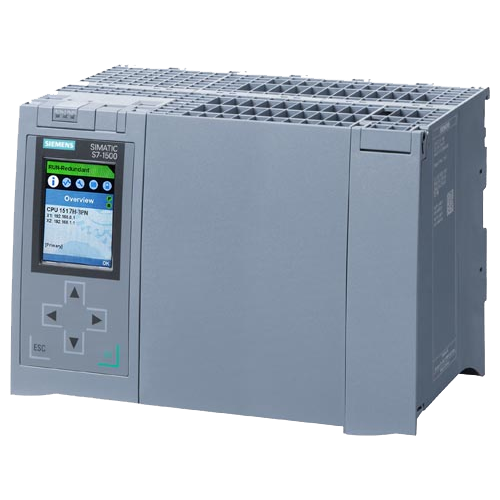
Overview
- Modular, scalable, and universally usable system in IP20 degree of protection
- The system solution for a variety of automation applications in discrete automation
- Highest performance with excellent usability
- Can only be configured in Totally Integrated Automation Portal with STEP 7 Professional V12 or higher
Performance
Increase in performance through;
- Faster command execution
- Language extensions
- New data types
- Faster backplane bus
- Optimised code generation
Powerful performance
- PROFINET IO (2-port switch) as standard interface; from CPU 1515-2 PN, one or more additional integrated PROFINET interfaces, e.g. for network separation, for connecting further PROFINET devices or for high-speed communication as an I-Device
- OPC UA server (data access) and client as runtime option for the easy connection of SIMATIC S7-1500 to non-Siemens devices/systems
- Expandable with communications modules for bus systems and point-to-point connection
Integrated technology
Motion control integrated without additional modules:
- Standardised blocks (PLCopen) for connection of analog and PROFIdrive-capable drives
- The Motion control functionality supports speed-controlled axes, positioning axes, relative synchronous operation (synchronising without specification of the synchronised position), as well as external encoders, cams and probes.
- Extended motion control functions such as absolute synchronous operation (synchronising with specification of the synchronised position), camming and functions for controlling kinematics are also integrated in the technology CPUs.
- Comprehensive trace functions for all CPU tags for real-time diagnostics and sporadic error detection;
- for effective commissioning and quick optimisation of drives and controls
- Comprehensive control functionalities:
- e.g. easily configurable blocks for automatic optimization of the control parameters for optimum control quality
- Additional functions through available technology modules:
- e.g. high-speed counting, position detection, or measurement functions for signals up to 1 MHz
Safely integrated
- Protection of personnel and machinery – within the framework of an integrated complete system
- Fail-safe SIMATIC S7-1500(T)F controllers for processing standard and safety programs on the same controller.
- The fail-safe and standard user programs are created in the TIA Portal with the same editors; fail-safe data, for example, can therefore be evaluated like standard data in the standard user program. Due to this integration the system benefits and the comprehensive functionality of SIMATIC are also available for fail-safe applications.
Redundant systems
CPU 1513R-1 PN, CPU 1515R-2 PN
CPU 1517H-3 PN/FO
- Redundant S7-1500R/H CPUs for applications where availability of the controller is crucial.
- Both CPUs are connected with the I/O stations via a PROFINET-IO ring. Synchronisation for the S7-1500R is via this ring, or via separate FOC synchronisation cables for the S7-1500H. In the event of a CPU failure, the back-up CPU automatically assumes control of the process. No data is lost and the process can be continued extremely quickly. The PROFINET IO ring ensures that all nodes remain accessible in the event of a fieldbus interruption.
- The engineering corresponds to that of a standard CPU. The TIA Portal and redundant CPUs handle the synchronisation of the programs and data. All without any additional overhead for the user.
SIMATIC S7-1500R mode of operation
Security Integrated
- Password-based know-how protection against unauthorised read-out and modification of program blocks
- Copy protection for greater protection against unauthorised copying of program blocks:
With copy protection, individual blocks on the SIMATIC memory card can be tied to its serial number so that the block can only be run if the configured memory card is inserted into the CPU. - Rights concept with four different authorisation levels:
Different access rights can be assigned to various user groups. The new protection level 4 makes it possible to also restrict communication to HMI devices. - Improved manipulation protection:
Changed or unauthorised transfers of engineering data are detected by the controller. - For use of an Ethernet CP (CP 1543-1):
- Additional access protection by means of a firewall
- Establishment of secure VPN connections
Design and Handling
- CPUs with display for plain text information (display simulator tool on the Internet):
- Information about article numbers, firmware version, and the serial number of all connected modules can be displayed
- Setting the IP address of the CPU and additional network settings possible directly on site, without programming device on the display
- Display of occurring error messages directly as plain text message, meaning reduction in downtime
- Uniform front connectors for all modules and integrated potential bridges for flexible potential group formation simplify stock keeping and reduce wiring effort
- Integrated DIN rail in the S7-1500 mounting rail: quick and easy installation of additional components such as miniature circuit breakers, relays, etc.
- Central expansion with signal modules: for flexible adaptation to any application
- System cabling for digital signal modules: for fast and clearly arranged connecting to sensors and actuators in the field and simple wiring inside the control cabinet
- Power supply:
- Load power supply modules (PMs) for supplying the module with 24 V
- Power supply modules to supply power to the internal module electronics via the backplane bus
- System power supply modules for retentively storing the entire work memory on the controller
- Distributed expansion:
- Use of up to 30 signal modules, communication modules, and technology modules via the PROFINET interface module IM 155-5 for the ET 200MP I/O system
- No difference in terms of handling and system functions in central and distributed operatio
Integrated System Diagnostics
Integrated system diagnostics for CPUs, activated by default:
- Consistent plain text display of system diagnostic information in the display, TIA Portal, HMI, and web server, even for drive messages. Messages are updated even if the CPU is in STOP state.
- System diagnostics integrated in the CPU firmware. Configuration by user not required. The diagnostics is automatically updated on configuration changes.
Support of SIMATIC ProDiag S7-1500
ProDiag is a concept for the easy creation of machine and plant diagnostics It increases availability and supports with fault analysis and elimination on-site.
Datalog (archives) and Recipes
SIMATIC memory card:
- Plug-in load memory
- Permits firmware updates
- Storage option for STEP 7 projects (including comments and symbols), additional documentation, or csv/ASCII files (for recipes and archives)
- Easy access to plant-relevant operating data and configuration data with Office tools via the SD card reader (two-way data exchange from and to the controller)
Integrated web server:
- Easy access to plant-relevant operating data and configuration data, motion control diagnostics and display of trace recordings via a web browser
Approvals
The SIMATIC S7-1500 complies with the following national and international standards:
- cULus approval
- cULus HazLoc approval
- FM approval
- ATEX approval (only for 24 V; not for 230 V)
- CE
- RCM (formerly C-Tick)
- KCC
- IECEx (24 V only; not for 230 V)
- EN 61000-6-4
- EN 60068-2-1/ -2/ -6/ -14/ -27/ -30/ -32
- EN 61131-2
You can find the marine approvals available for the S7-1500 online (SIMATIC Customer Support): http://www.siemens.com/automation/support
The S7-1500 system is also suitable for operating at elevations up to 5000 m. Here is a List of all currently approved modules:
Catalog ST 70:
You can also find information about SIMATIC S7-1500 in the Catalog ST 70: http://www.automation.siemens.com/salesmaterial-as/catalog/en/simatic-st70-chap04-english-2019.pdf
Application
The SIMATIC S7-1500 is a modular control system for a variety of automation applications in discrete automation.
The modular and fan-free design, simple implementation of distributed structures, and convenient handling make the SIMATIC S7-1500 the cost-effective and user-friendly solution for a wide range of diverse tasks.
Application areas of the SIMATIC S7-1500 include:
- Special machinery
- Textile machines
- Packaging machinery
- Pick-and-place machines
- Assembly machines
- Palleting machines
- General mechanical equipment manufacture
- Controller building
- Machine tool manufacture
- Installation systems,
- Electrical/electronics industry and the skilled trades
- Automotive
- Water/wastewater
- Food & beverage
- Infrastructure (tunnels, traffic control, marine, airports, etc.)
Several CPUs of different performance levels and a comprehensive module range with many convenient functions are available. Failsafe CPUs facilitate use in failsafe applications. The modular design allows users to use only the modules they require for their applications. In the case of task expansions, the controller can be upgraded at any time by means of additional modules:
Excellent industrial compatibility thanks to high electromagnetic compatibility and resistance to shock and vibration enable universal use of the SIMATIC S7-1500.
Design
General
An S7-1500 automation system has a modular design and comprises up to 32 modules. It has a comprehensive range of modules that can be combined individually. The S7-1500 automation system supports one-tier configurations where all modules are mounted on one DIN rail (see Manual for requirements).
A system includes the following:
- Controller: CPUs with different grades of performance with integrated PROFINET interface, or PROFINET and PROFIBUS interface, for connection of distributed I/O and for communication between programming device, operator panel, other SIMATIC controllers or third-party devices.
Various CPU versions are available for SIMATIC S7-1500:- Standard CPUs (as MFP version: capable of executing C/C++ code on the controller)
- Compact CPUs with digital and analog inputs and outputs as well as counter inputs and high-speed outputs for integrated technological functions direct on the CPU
- Fail-safe CPUs (as MFP version: capable of executing C/C++ code on the controller) for the execution of standard and safety-related programs on the same computer
- Technology CPUs with extended Motion Control functions such as absolute synchronous operation (synchronising with specification of the synchronised position), camming and functions for controlling kinematics.
- Signal modules for digital and analog inputs/outputs.
- Technology modules, e.g. for high-speed counting, position detection, or measurement functions.
- Communication modules and communications processors for expansion of controllers by communications interfaces
The following can also be used depending on requirements:
- Power supply modules (PS), to supply the internal electronics of the S7-1500 modules via the backplane bus, in case the output of the CPU to the backplane bus is not sufficient for all connected modules. In addition, the 60 W 24/48/60 V DC HF PS enables the CPU to retentively store its entire work memory for data.
- Load power supply modules (PMs) for connecting the SIMATIC S7-1500 to a supply voltage of 120/230 V AC.
- Interface modules to connect distributed I/O based on S7-1500.
Design
The simple design makes the SIMATIC S7-1500 versatile and service-friendly.
- Integrated backplane bus:
The backplane bus is integrated into the modules. The modules are connected via U connectors plugged into the rear of the enclosures. This saves time during installation. - Module assembly on S7-1500 mounting rails:
available in various lengths, including a version for cutting to length. A wide range of standard components such as additional terminals, miniature circuit breakers, or small relays can be snapped on due to the integrated DIN rail. - Reliable and user-friendly wiring:
- The I/O signals are connected via a uniform 40-pole front connector. The mechanical coding between the signal module and front connector prevents destruction of the electronics by accidental incorrect insertion.
- For simple wiring of the front connector, it can be placed in the “prewiring position”. In this position, the plug has no contact with the module electronics yet. This position can also be used to make changes during operation. The user is supported by a printed cabling diagram on the inside of the front flap.
- Front connectors are available as versions with screw-type terminals or push-in terminals. Both versions permit the connection of wires with a core cross-section from 0.25 mm2 to 1.5 mm2 (AWG 24 to AWG 16).
- In addition, system wiring via TOP Connect is available for digital signal modules. It allows the quick and clearly arranged connection to sensors and actuators from the field as well as simple wiring within the control cabinet.
- For analog modules, the shielding can take place direct on the module; a shield connection set that can be installed without tools is included with the module.
- Plant-specific labeling:
Labeling strips are available for the signal modules of the SIMATIC S7-1500. These DIN A4 sheets can be labeled using a standard laser printer. Automatic printing is possible from the TIA Portal without having to re-enter the symbols or addresses. The labeling strips are designed such that there is a 1:1 assignment of the labeling for channel or diagnostics display. If the front flap is opened, this 1:1 assignment of diagnostics display to terminal is retained. - Variable and scalable station setup:
- Signal modules and communication modules can be inserted in any way without restrictions. The system configures itself.
- The maximum configuration comprises the CPU with 31 modules (30 modules + 1 power supply). The power supply (PS) is required to supply the internal electronics of the S7-1500 modules via the backplane bus, in case the output of the CPU to the backplane bus is not sufficient for all connected modules.
- Compact dimensions:
SIMATIC S7-1500 is dimensioned so that it fits perfectly in the installation space of a SIMATIC S7-300 controller or ET 200M I/O system. - Flexible installation:
The SIMATIC S7-1500 and its modules can be installed both vertically and horizontally to provide an optimum fit to the available space.
I/O Modules
The following module types are available for use on a SIMATIC S7-1500/ET 200MP:
- Standard and fail-safe digital input modules
- Standard and fail-safe digital output modules
- Digital input/output modules
- Analog input modules
- Analog input/output modules
- Analog output modules
- Including high-speed (HS) analog modules with a basic execution time of 62.5 µs, regardless of the number of activated channels
- Technology modules for counting and positioning
- Communication modules for IO-Link and point-to-point communication and bus connection
Various module classes are available to provide users with optimum scalability in their application. The modules themselves are labeled accordingly:
- BA (Basic): Simple, cost-effective modules, without diagnostics and without parameters
- ST (Standard): Modules with module-specific or load group-specific diagnostics and, if applicable, with parameters; for analog modules: accuracy class 0.3%
- HF (High Feature): Modules with channel-specific diagnostics and parameter setting as well as support for isosynchronous mode; for analog modules: accuracy class 0.1%, increased immunity and galvanic isolation
- HS (High Speed): Modules with extremely short filter and conversion times for very fast applications as well as support for isosynchronous mode; e.g. 8-channel analog modules with a basic execution time of 62.5 µs, regardless of the number of activated channels.
Accessories for I/O modules:
- Labeling sheets:
For insertion in the I/O modules (10 DIN A4 sheets with 10 strips each, pre-perforated, for printing with a standard laser printer; available colour: Al grey) - Shield connection:
A simple shield connection set that can be installed without tools is available for the SIMATIC S7-1500 system (analog modules and technology modules). This consists of a 24 V DC infeed element, a shield clamp, and a universal shield terminal. The latter is designed so that it can be used for a single thin trunk cable, several thin trunk cables, or a thick trunk cable. Consistent separation of 24 V DC infeed and measurement signals as well as a low-impedance connection between shield and signal cables ensure high EMC stability and high resistance to interference. - Uniform 40-pole front connector
- Additional accessories such as the front doors for the I/O modules or the U connectors for the self-assembling backplane bus
Communication
- PROFINET IO IRT interface (2-port switch), integrated in the CPU (PROFINET RT only for S7-1500R/H); for defined response times and high-precision plant behaviour.
- Communications processors for connecting to the PROFIBUS, Industrial Ethernet and PROFINET bus systems
- Communication modules for point-to-point connections.
From CPU 1515, all CPUs feature one or more additional integrated PROFINET interfaces with separate IP address, e.g. for network separation or for connecting additional PROFINET IO devices. From CPU 1516-3 PN/DP, PROFIBUS nodes can be connected via the integrated PROFIBUS interface. The CPUs without integrated PROFIBUS interface can be easily expanded via a PROFIBUS CM.
Process communication via PROFINET IO
The SIMATIC S7-1500 is connected to the PROFINET IO bus system via the integrated PROFINET interface and permits a distributed automation configuration with defined response times and high-precision plant behaviour.
The distributed I/O via PROFINET IO is treated just like a centralised I/O from the user’s perspective (same configuring, addressing, and programming).
The following can be connected as IO controllers:
- SIMATIC S7-1500
- SIMATIC S7-1200
- SIMATIC S7-300 (via CPUs with PROFINET interface or PROFINET CPs)
- SIMATIC S7-400 (via CPUs with PROFINET interface or PROFINET CPs)
- SIMATIC ET 200 (via CPUs with PROFINET interface)
The following can be connected as an I-device or device:
- SIMATIC S7-1500
- SIMATIC S7-1200 (FW 4.0 or higher)
- ET 200S IM151-8 PN/DP CPU, ET 200pro IM154-8 PN/DP CPU
- ET 200SP CPU 1510SP-1 PN, CPU 1512SP-1 PN
- SIMATIC S7-300 (via CPUs with PROFINET interface or PROFINET CPs)
- SIMATIC S7-400 (via CPUs with PROFINET interface or PROFINET CPs)
- ET 200 distributed I/O devices
- HMI devices which are operated as direct key modules
- Field devices
Process communication via PROFIBUS DP
SIMATIC S7-1500 (not S7-155R/H) is connected to the PROFIBUS DP bus system via a communications module or via CPUs with integrated PROFIBUS DP interfaces. The CPUs or communication modules with PROFIBUS DP interface enable distributed automation configuration with high speed and simple handling.
The distributed I/O via PROFIBUS DP is treated just like a centralized I/O from the user’s perspective (same configuring, addressing, and programming).
The following can be connected as masters:
- SIMATIC S7-1500 (not S7-1500R/H)
(via CPUs with PROFIBUS DP interface or PROFIBUS DP communications modules) - SIMATIC S7-300
(via CPUs with PROFIBUS DP interface or PROFIBUS DP CPs) - SIMATIC S7-400
(via CPUs with PROFIBUS DP interface or PROFIBUS DP CPs) - SIMATIC S5-115U/H, S5-135U and S5-155U/H with IM 308
- SIMATIC 505
The following can be connected as a slave or as an I-slave:
- Distributed I/O devices, e.g. ET 200
- Field devices
- SIMATIC S7-200, S7-1200, S7-300
- C7-633/P DP, C7-633 DP, C7-634/P DP, C7-634 DP, C7-626 DP
- SIMATIC S7-400 (via CP 443-5 only)
- SIMATIC S7-1500 (via CP/CM 1542-5 only)
Data communication via Ethernet
The S7-1500 can be connected to the Industrial Ethernet bus system via the integrated PROFINET interface or via a communication module.
The following can be connected:
- SIMATIC S7-1200
- SIMATIC S7-1500
- SIMATIC S7-300
- SIMATIC S7-400
- SIMATIC S5-115U/H, S5-135U, S5-155U/H
- Programming devices
- PCs, industrial PCs
- SIMATIC HMI human machine interface systems
- Numerical controls
- Robot controls
- Drive controls
- Devices of other manufacturers
Protocols supported:
- TCP/IP
- ISO-on-TCP (RFC1006)
- UDP
- SNMP
- DCP
- LLDP
- HTTP
- HTTPS
- MODBUS TCP
- OPC UA
The Industrial Ethernet CP 1543-1 offers the following additional functionalities:
- 1 Gbit interface
- IPv6 support
- Security: access protection by means of hardware identification, IP/MAC access list, firewall, VPN tunnel
- Communication with S5 systems via the ISO protocol
- FTP (client/server), email, SNMPv1/v3
Data communication via PROFIBUS
SIMATIC S7-1500 (not S7-1500R/H) can be connected to the PROFIBUS bus system via a communications module or via the CPUs with integrated PROFIBUS DP interfaces. The following can be connected:
- SIMATIC S7-1200
- SIMATIC S7-1500
- SIMATIC S7-300
- SIMATIC S7-400
- SIMATIC S5-115U/H, S5-135U, S5-155U/H
- Programming devices
- PCs, industrial PCs
- SIMATIC HMI human machine interface systems
- Numerical controls
- Robot controls
- Drive controls
- Devices of other manufacturers
Data communication via point-to-point communication modules
Powerful point-to-point connections can be implemented via the point-to-point communication modules. The following can be connected, for example:
- SIMATIC S7 and SIMATIC S5 automation systems and non-Siemens systems
- Scanners, barcode readers, identification systems
- Robot controls
- Printers
Protocols supported:
- Freeport: user-parameterizable telegram format for universal communication
- 3964(R) for improved transmission reliability
- Modbus RTU Master
- Modbus RTU Slave
- USS, implemented through instructions
Interface properties:
- RS 232 with auxiliary signals
- RS 422 for full-duplex connections
- RS 485 for half-duplex and multi-point connections
- Transmission rates from 300 to 115 200 bit/s
- Connection via sub D connector
Data communication via IO-Link communication modules
Up to eight IO-Link devices can be connected via the CM 8xIO-Link communication module.- IO-Link Master according to IO-Link specification V1.1
- Data transmission rates COM1 (4.8 kBd), COM2 (38.4 kBd), COM3 (230.4 kBd)
- Parameterizable diagnostics can be set for each channel
- Master backup with “IO_LINK_MASTER_8” function block
- Replacement of IO-Link devices (only for V1.1 devices)
- Supports firmware updates for IO-Link devices
- Variable address range for I/O data with up to 240 byte inputs and 240 byte outputs
Expansion limits:
-
- Max. 32 bytes of input and output data per port
- Max. 240 bytes of input and output data per module
- Port Qualifier Information (PQI)
- IO-Link port configuration with S7-PCT
- IO-Link port configuration with STEP 7 or GSD (without S7-PCT)
Function
Performance
An S7-1500 automation system has a modular design and comprises up to 32 modules. It has a comprehensive range of modules that can be combined individually. The S7-1500 automation system supports one-tier configurations where all modules are mounted on one DIN rail (see Manual for requirements).
A system includes the following:
- Controller: CPUs with different grades of performance with integrated PROFINET interface, or PROFINET and PROFIBUS interface, for connection of distributed I/O and for communication between programming device, operator panel, other SIMATIC controllers or third-party devices.
Various CPU versions are available for SIMATIC S7-1500:- Standard CPUs (as MFP version: capable of executing C/C++ code on the controller)
- Compact CPUs with digital and analog inputs and outputs as well as counter inputs and high-speed outputs for integrated technological functions direct on the CPU
- Fail-safe CPUs (as MFP version: capable of executing C/C++ code on the controller) for the execution of standard and safety-related programs on the same computer
- Technology CPUs with extended Motion Control functions such as absolute synchronous operation (synchronising with specification of the synchronised position), camming and functions for controlling kinematics.
- Signal modules for digital and analog inputs/outputs.
- Technology modules, e.g. for high-speed counting, position detection, or measurement functions.
- Communication modules and communications processors for expansion of controllers by communications interfaces
The following can also be used depending on requirements:
- Power supply modules (PS), to supply the internal electronics of the S7-1500 modules via the backplane bus, in case the output of the CPU to the backplane bus is not sufficient for all connected modules. In addition, the 60 W 24/48/60 V DC HF PS enables the CPU to retentively store its entire work memory for data.
- Load power supply modules (PMs) for connecting the SIMATIC S7-1500 to a supply voltage of 120/230 V AC.
- Interface modules to connect distributed I/O based on S7-1500.
Integrated technology (not S7-1500R/H)
The simple design makes the SIMATIC S7-1500 versatile and service-friendly.
- Integrated backplane bus:
The backplane bus is integrated into the modules. The modules are connected via U connectors plugged into the rear of the enclosures. This saves time during installation. - Module assembly on S7-1500 mounting rails:
available in various lengths, including a version for cutting to length. A wide range of standard components such as additional terminals, miniature circuit breakers, or small relays can be snapped on due to the integrated DIN rail. - Reliable and user-friendly wiring:
- The I/O signals are connected via a uniform 40-pole front connector. The mechanical coding between the signal module and front connector prevents destruction of the electronics by accidental incorrect insertion.
- For simple wiring of the front connector, it can be placed in the “prewiring position”. In this position, the plug has no contact with the module electronics yet. This position can also be used to make changes during operation. The user is supported by a printed cabling diagram on the inside of the front flap.
- Front connectors are available as versions with screw-type terminals or push-in terminals. Both versions permit the connection of wires with a core cross-section from 0.25 mm2 to 1.5 mm2 (AWG 24 to AWG 16).
- In addition, system wiring via TOP Connect is available for digital signal modules. It allows the quick and clearly arranged connection to sensors and actuators from the field as well as simple wiring within the control cabinet.
- For analog modules, the shielding can take place direct on the module; a shield connection set that can be installed without tools is included with the module.
- Plant-specific labeling:
Labeling strips are available for the signal modules of the SIMATIC S7-1500. These DIN A4 sheets can be labeled using a standard laser printer. Automatic printing is possible from the TIA Portal without having to re-enter the symbols or addresses. The labeling strips are designed such that there is a 1:1 assignment of the labeling for channel or diagnostics display. If the front flap is opened, this 1:1 assignment of diagnostics display to terminal is retained. - Variable and scalable station setup:
- Signal modules and communication modules can be inserted in any way without restrictions. The system configures itself.
- The maximum configuration comprises the CPU with 31 modules (30 modules + 1 power supply). The power supply (PS) is required to supply the internal electronics of the S7-1500 modules via the backplane bus, in case the output of the CPU to the backplane bus is not sufficient for all connected modules.
- Compact dimensions:
SIMATIC S7-1500 is dimensioned so that it fits perfectly in the installation space of a SIMATIC S7-300 controller or ET 200M I/O system. - Flexible installation:
The SIMATIC S7-1500 and its modules can be installed both vertically and horizontally to provide an optimum fit to the available space.
Isochronous mode (not S7-1500R/H)
The following module types are available for use on a SIMATIC S7-1500/ET 200MP:
- Standard and fail-safe digital input modules
- Standard and fail-safe digital output modules
- Digital input/output modules
- Analog input modules
- Analog input/output modules
- Analog output modules
- Including high-speed (HS) analog modules with a basic execution time of 62.5 µs, regardless of the number of activated channels
- Technology modules for counting and positioning
- Communication modules for IO-Link and point-to-point communication and bus connection
Various module classes are available to provide users with optimum scalability in their application. The modules themselves are labeled accordingly:
- BA (Basic): Simple, cost-effective modules, without diagnostics and without parameters
- ST (Standard): Modules with module-specific or load group-specific diagnostics and, if applicable, with parameters; for analog modules: accuracy class 0.3%
- HF (High Feature): Modules with channel-specific diagnostics and parameter setting as well as support for isosynchronous mode; for analog modules: accuracy class 0.1%, increased immunity and galvanic isolation
- HS (High Speed): Modules with extremely short filter and conversion times for very fast applications as well as support for isosynchronous mode; e.g. 8-channel analog modules with a basic execution time of 62.5 µs, regardless of the number of activated channels.
Accessories for I/O modules:
- Labeling sheets:
For insertion in the I/O modules (10 DIN A4 sheets with 10 strips each, pre-perforated, for printing with a standard laser printer; available colour: Al grey) - Shield connection:
A simple shield connection set that can be installed without tools is available for the SIMATIC S7-1500 system (analog modules and technology modules). This consists of a 24 V DC infeed element, a shield clamp, and a universal shield terminal. The latter is designed so that it can be used for a single thin trunk cable, several thin trunk cables, or a thick trunk cable. Consistent separation of 24 V DC infeed and measurement signals as well as a low-impedance connection between shield and signal cables ensure high EMC stability and high resistance to interference. - Uniform 40-pole front connector
- Additional accessories such as the front doors for the I/O modules or the U connectors for the self-assembling backplane bus
Security Integrated
- PROFINET IO IRT interface (2-port switch), integrated in the CPU (PROFINET RT only for S7-1500R/H); for defined response times and high-precision plant behaviour.
- Communications processors for connecting to the PROFIBUS, Industrial Ethernet and PROFINET bus systems
- Communication modules for point-to-point connections.
From CPU 1515, all CPUs feature one or more additional integrated PROFINET interfaces with separate IP address, e.g. for network separation or for connecting additional PROFINET IO devices. From CPU 1516-3 PN/DP, PROFIBUS nodes can be connected via the integrated PROFIBUS interface. The CPUs without integrated PROFIBUS interface can be easily expanded via a PROFIBUS CM.
Process communication via PROFINET IO
The SIMATIC S7-1500 is connected to the PROFINET IO bus system via the integrated PROFINET interface and permits a distributed automation configuration with defined response times and high-precision plant behaviour.
The distributed I/O via PROFINET IO is treated just like a centralised I/O from the user’s perspective (same configuring, addressing, and programming).
The following can be connected as IO controllers:
- SIMATIC S7-1500
- SIMATIC S7-1200
- SIMATIC S7-300 (via CPUs with PROFINET interface or PROFINET CPs)
- SIMATIC S7-400 (via CPUs with PROFINET interface or PROFINET CPs)
- SIMATIC ET 200 (via CPUs with PROFINET interface)
The following can be connected as an I-device or device:
- SIMATIC S7-1500
- SIMATIC S7-1200 (FW 4.0 or higher)
- ET 200S IM151-8 PN/DP CPU, ET 200pro IM154-8 PN/DP CPU
- ET 200SP CPU 1510SP-1 PN, CPU 1512SP-1 PN
- SIMATIC S7-300 (via CPUs with PROFINET interface or PROFINET CPs)
- SIMATIC S7-400 (via CPUs with PROFINET interface or PROFINET CPs)
- ET 200 distributed I/O devices
- HMI devices which are operated as direct key modules
- Field devices
Process communication via PROFIBUS DP
SIMATIC S7-1500 (not S7-155R/H) is connected to the PROFIBUS DP bus system via a communications module or via CPUs with integrated PROFIBUS DP interfaces. The CPUs or communication modules with PROFIBUS DP interface enable distributed automation configuration with high speed and simple handling.
The distributed I/O via PROFIBUS DP is treated just like a centralized I/O from the user’s perspective (same configuring, addressing, and programming).
The following can be connected as masters:
- SIMATIC S7-1500 (not S7-1500R/H)
(via CPUs with PROFIBUS DP interface or PROFIBUS DP communications modules) - SIMATIC S7-300
(via CPUs with PROFIBUS DP interface or PROFIBUS DP CPs) - SIMATIC S7-400
(via CPUs with PROFIBUS DP interface or PROFIBUS DP CPs) - SIMATIC S5-115U/H, S5-135U and S5-155U/H with IM 308
- SIMATIC 505
The following can be connected as a slave or as an I-slave:
- Distributed I/O devices, e.g. ET 200
- Field devices
- SIMATIC S7-200, S7-1200, S7-300
- C7-633/P DP, C7-633 DP, C7-634/P DP, C7-634 DP, C7-626 DP
- SIMATIC S7-400 (via CP 443-5 only)
- SIMATIC S7-1500 (via CP/CM 1542-5 only)
Data communication via Ethernet
The S7-1500 can be connected to the Industrial Ethernet bus system via the integrated PROFINET interface or via a communication module.
The following can be connected:
- SIMATIC S7-1200
- SIMATIC S7-1500
- SIMATIC S7-300
- SIMATIC S7-400
- SIMATIC S5-115U/H, S5-135U, S5-155U/H
- Programming devices
- PCs, industrial PCs
- SIMATIC HMI human machine interface systems
- Numerical controls
- Robot controls
- Drive controls
- Devices of other manufacturers
Protocols supported:
- TCP/IP
- ISO-on-TCP (RFC1006)
- UDP
- SNMP
- DCP
- LLDP
- HTTP
- HTTPS
- MODBUS TCP
- OPC UA
The Industrial Ethernet CP 1543-1 offers the following additional functionalities:
- 1 Gbit interface
- IPv6 support
- Security: access protection by means of hardware identification, IP/MAC access list, firewall, VPN tunnel
- Communication with S5 systems via the ISO protocol
- FTP (client/server), email, SNMPv1/v3
Data communication via PROFIBUS
SIMATIC S7-1500 (not S7-1500R/H) can be connected to the PROFIBUS bus system via a communications module or via the CPUs with integrated PROFIBUS DP interfaces. The following can be connected:
- SIMATIC S7-1200
- SIMATIC S7-1500
- SIMATIC S7-300
- SIMATIC S7-400
- SIMATIC S5-115U/H, S5-135U, S5-155U/H
- Programming devices
- PCs, industrial PCs
- SIMATIC HMI human machine interface systems
- Numerical controls
- Robot controls
- Drive controls
- Devices of other manufacturers
Data communication via point-to-point communication modules
Powerful point-to-point connections can be implemented via the point-to-point communication modules. The following can be connected, for example:
- SIMATIC S7 and SIMATIC S5 automation systems and non-Siemens systems
- Scanners, barcode readers, identification systems
- Robot controls
- Printers
Protocols supported:
- Freeport: user-parameterizable telegram format for universal communication
- 3964(R) for improved transmission reliability
- Modbus RTU Master
- Modbus RTU Slave
- USS, implemented through instructions
Interface properties:
- RS 232 with auxiliary signals
- RS 422 for full-duplex connections
- RS 485 for half-duplex and multi-point connections
- Transmission rates from 300 to 115 200 bit/s
- Connection via sub D connector
Data communication via IO-Link communication modules
Up to eight IO-Link devices can be connected via the CM 8xIO-Link communication module.- IO-Link Master according to IO-Link specification V1.1
- Data transmission rates COM1 (4.8 kBd), COM2 (38.4 kBd), COM3 (230.4 kBd)
- Parameterizable diagnostics can be set for each channel
- Master backup with “IO_LINK_MASTER_8” function block
- Replacement of IO-Link devices (only for V1.1 devices)
- Supports firmware updates for IO-Link devices
- Variable address range for I/O data with up to 240 byte inputs and 240 byte outputs
Expansion limits:
-
- Max. 32 bytes of input and output data per port
- Max. 240 bytes of input and output data per module
- Port Qualifier Information (PQI)
- IO-Link port configuration with S7-PCT
- IO-Link port configuration with STEP 7 or GSD (without S7-PCT)
Design and handling
- PROFINET IO IRT interface (2-port switch), integrated in the CPU (PROFINET RT only for S7-1500R/H); for defined response times and high-precision plant behaviour.
- Communications processors for connecting to the PROFIBUS, Industrial Ethernet and PROFINET bus systems
- Communication modules for point-to-point connections.
From CPU 1515, all CPUs feature one or more additional integrated PROFINET interfaces with separate IP address, e.g. for network separation or for connecting additional PROFINET IO devices. From CPU 1516-3 PN/DP, PROFIBUS nodes can be connected via the integrated PROFIBUS interface. The CPUs without integrated PROFIBUS interface can be easily expanded via a PROFIBUS CM.
Process communication via PROFINET IO
The SIMATIC S7-1500 is connected to the PROFINET IO bus system via the integrated PROFINET interface and permits a distributed automation configuration with defined response times and high-precision plant behaviour.
The distributed I/O via PROFINET IO is treated just like a centralised I/O from the user’s perspective (same configuring, addressing, and programming).
The following can be connected as IO controllers:
- SIMATIC S7-1500
- SIMATIC S7-1200
- SIMATIC S7-300 (via CPUs with PROFINET interface or PROFINET CPs)
- SIMATIC S7-400 (via CPUs with PROFINET interface or PROFINET CPs)
- SIMATIC ET 200 (via CPUs with PROFINET interface)
The following can be connected as an I-device or device:
- SIMATIC S7-1500
- SIMATIC S7-1200 (FW 4.0 or higher)
- ET 200S IM151-8 PN/DP CPU, ET 200pro IM154-8 PN/DP CPU
- ET 200SP CPU 1510SP-1 PN, CPU 1512SP-1 PN
- SIMATIC S7-300 (via CPUs with PROFINET interface or PROFINET CPs)
- SIMATIC S7-400 (via CPUs with PROFINET interface or PROFINET CPs)
- ET 200 distributed I/O devices
- HMI devices which are operated as direct key modules
- Field devices
Process communication via PROFIBUS DP
SIMATIC S7-1500 (not S7-155R/H) is connected to the PROFIBUS DP bus system via a communications module or via CPUs with integrated PROFIBUS DP interfaces. The CPUs or communication modules with PROFIBUS DP interface enable distributed automation configuration with high speed and simple handling.
The distributed I/O via PROFIBUS DP is treated just like a centralized I/O from the user’s perspective (same configuring, addressing, and programming).
The following can be connected as masters:
- SIMATIC S7-1500 (not S7-1500R/H)
(via CPUs with PROFIBUS DP interface or PROFIBUS DP communications modules) - SIMATIC S7-300
(via CPUs with PROFIBUS DP interface or PROFIBUS DP CPs) - SIMATIC S7-400
(via CPUs with PROFIBUS DP interface or PROFIBUS DP CPs) - SIMATIC S5-115U/H, S5-135U and S5-155U/H with IM 308
- SIMATIC 505
The following can be connected as a slave or as an I-slave:
- Distributed I/O devices, e.g. ET 200
- Field devices
- SIMATIC S7-200, S7-1200, S7-300
- C7-633/P DP, C7-633 DP, C7-634/P DP, C7-634 DP, C7-626 DP
- SIMATIC S7-400 (via CP 443-5 only)
- SIMATIC S7-1500 (via CP/CM 1542-5 only)
Data communication via Ethernet
The S7-1500 can be connected to the Industrial Ethernet bus system via the integrated PROFINET interface or via a communication module.
The following can be connected:
- SIMATIC S7-1200
- SIMATIC S7-1500
- SIMATIC S7-300
- SIMATIC S7-400
- SIMATIC S5-115U/H, S5-135U, S5-155U/H
- Programming devices
- PCs, industrial PCs
- SIMATIC HMI human machine interface systems
- Numerical controls
- Robot controls
- Drive controls
- Devices of other manufacturers
Protocols supported:
- TCP/IP
- ISO-on-TCP (RFC1006)
- UDP
- SNMP
- DCP
- LLDP
- HTTP
- HTTPS
- MODBUS TCP
- OPC UA
The Industrial Ethernet CP 1543-1 offers the following additional functionalities:
- 1 Gbit interface
- IPv6 support
- Security: access protection by means of hardware identification, IP/MAC access list, firewall, VPN tunnel
- Communication with S5 systems via the ISO protocol
- FTP (client/server), email, SNMPv1/v3
Data communication via PROFIBUS
SIMATIC S7-1500 (not S7-1500R/H) can be connected to the PROFIBUS bus system via a communications module or via the CPUs with integrated PROFIBUS DP interfaces. The following can be connected:
- SIMATIC S7-1200
- SIMATIC S7-1500
- SIMATIC S7-300
- SIMATIC S7-400
- SIMATIC S5-115U/H, S5-135U, S5-155U/H
- Programming devices
- PCs, industrial PCs
- SIMATIC HMI human machine interface systems
- Numerical controls
- Robot controls
- Drive controls
- Devices of other manufacturers
Data communication via point-to-point communication modules
Powerful point-to-point connections can be implemented via the point-to-point communication modules. The following can be connected, for example:
- SIMATIC S7 and SIMATIC S5 automation systems and non-Siemens systems
- Scanners, barcode readers, identification systems
- Robot controls
- Printers
Protocols supported:
- Freeport: user-parameterizable telegram format for universal communication
- 3964(R) for improved transmission reliability
- Modbus RTU Master
- Modbus RTU Slave
- USS, implemented through instructions
Interface properties:
- RS 232 with auxiliary signals
- RS 422 for full-duplex connections
- RS 485 for half-duplex and multi-point connections
- Transmission rates from 300 to 115 200 bit/s
- Connection via sub D connector
Data communication via IO-Link communication modules
Up to eight IO-Link devices can be connected via the CM 8xIO-Link communication module.- IO-Link Master according to IO-Link specification V1.1
- Data transmission rates COM1 (4.8 kBd), COM2 (38.4 kBd), COM3 (230.4 kBd)
- Parameterizable diagnostics can be set for each channel
- Master backup with “IO_LINK_MASTER_8” function block
- Replacement of IO-Link devices (only for V1.1 devices)
- Supports firmware updates for IO-Link devices
- Variable address range for I/O data with up to 240 byte inputs and 240 byte outputs
Expansion limits:
-
- Max. 32 bytes of input and output data per port
- Max. 240 bytes of input and output data per module
- Port Qualifier Information (PQI)
- IO-Link port configuration with S7-PCT
- IO-Link port configuration with STEP 7 or GSD (without S7-PCT)
Integrated system diagnostics
- PROFINET IO IRT interface (2-port switch), integrated in the CPU (PROFINET RT only for S7-1500R/H); for defined response times and high-precision plant behaviour.
- Communications processors for connecting to the PROFIBUS, Industrial Ethernet and PROFINET bus systems
- Communication modules for point-to-point connections.
From CPU 1515, all CPUs feature one or more additional integrated PROFINET interfaces with separate IP address, e.g. for network separation or for connecting additional PROFINET IO devices. From CPU 1516-3 PN/DP, PROFIBUS nodes can be connected via the integrated PROFIBUS interface. The CPUs without integrated PROFIBUS interface can be easily expanded via a PROFIBUS CM.
Process communication via PROFINET IO
The SIMATIC S7-1500 is connected to the PROFINET IO bus system via the integrated PROFINET interface and permits a distributed automation configuration with defined response times and high-precision plant behaviour.
The distributed I/O via PROFINET IO is treated just like a centralised I/O from the user’s perspective (same configuring, addressing, and programming).
The following can be connected as IO controllers:
- SIMATIC S7-1500
- SIMATIC S7-1200
- SIMATIC S7-300 (via CPUs with PROFINET interface or PROFINET CPs)
- SIMATIC S7-400 (via CPUs with PROFINET interface or PROFINET CPs)
- SIMATIC ET 200 (via CPUs with PROFINET interface)
The following can be connected as an I-device or device:
- SIMATIC S7-1500
- SIMATIC S7-1200 (FW 4.0 or higher)
- ET 200S IM151-8 PN/DP CPU, ET 200pro IM154-8 PN/DP CPU
- ET 200SP CPU 1510SP-1 PN, CPU 1512SP-1 PN
- SIMATIC S7-300 (via CPUs with PROFINET interface or PROFINET CPs)
- SIMATIC S7-400 (via CPUs with PROFINET interface or PROFINET CPs)
- ET 200 distributed I/O devices
- HMI devices which are operated as direct key modules
- Field devices
Process communication via PROFIBUS DP
SIMATIC S7-1500 (not S7-155R/H) is connected to the PROFIBUS DP bus system via a communications module or via CPUs with integrated PROFIBUS DP interfaces. The CPUs or communication modules with PROFIBUS DP interface enable distributed automation configuration with high speed and simple handling.
The distributed I/O via PROFIBUS DP is treated just like a centralized I/O from the user’s perspective (same configuring, addressing, and programming).
The following can be connected as masters:
- SIMATIC S7-1500 (not S7-1500R/H)
(via CPUs with PROFIBUS DP interface or PROFIBUS DP communications modules) - SIMATIC S7-300
(via CPUs with PROFIBUS DP interface or PROFIBUS DP CPs) - SIMATIC S7-400
(via CPUs with PROFIBUS DP interface or PROFIBUS DP CPs) - SIMATIC S5-115U/H, S5-135U and S5-155U/H with IM 308
- SIMATIC 505
The following can be connected as a slave or as an I-slave:
- Distributed I/O devices, e.g. ET 200
- Field devices
- SIMATIC S7-200, S7-1200, S7-300
- C7-633/P DP, C7-633 DP, C7-634/P DP, C7-634 DP, C7-626 DP
- SIMATIC S7-400 (via CP 443-5 only)
- SIMATIC S7-1500 (via CP/CM 1542-5 only)
Data communication via Ethernet
The S7-1500 can be connected to the Industrial Ethernet bus system via the integrated PROFINET interface or via a communication module.
The following can be connected:
- SIMATIC S7-1200
- SIMATIC S7-1500
- SIMATIC S7-300
- SIMATIC S7-400
- SIMATIC S5-115U/H, S5-135U, S5-155U/H
- Programming devices
- PCs, industrial PCs
- SIMATIC HMI human machine interface systems
- Numerical controls
- Robot controls
- Drive controls
- Devices of other manufacturers
Protocols supported:
- TCP/IP
- ISO-on-TCP (RFC1006)
- UDP
- SNMP
- DCP
- LLDP
- HTTP
- HTTPS
- MODBUS TCP
- OPC UA
The Industrial Ethernet CP 1543-1 offers the following additional functionalities:
- 1 Gbit interface
- IPv6 support
- Security: access protection by means of hardware identification, IP/MAC access list, firewall, VPN tunnel
- Communication with S5 systems via the ISO protocol
- FTP (client/server), email, SNMPv1/v3
Data communication via PROFIBUS
SIMATIC S7-1500 (not S7-1500R/H) can be connected to the PROFIBUS bus system via a communications module or via the CPUs with integrated PROFIBUS DP interfaces. The following can be connected:
- SIMATIC S7-1200
- SIMATIC S7-1500
- SIMATIC S7-300
- SIMATIC S7-400
- SIMATIC S5-115U/H, S5-135U, S5-155U/H
- Programming devices
- PCs, industrial PCs
- SIMATIC HMI human machine interface systems
- Numerical controls
- Robot controls
- Drive controls
- Devices of other manufacturers
Data communication via point-to-point communication modules
Powerful point-to-point connections can be implemented via the point-to-point communication modules. The following can be connected, for example:
- SIMATIC S7 and SIMATIC S5 automation systems and non-Siemens systems
- Scanners, barcode readers, identification systems
- Robot controls
- Printers
Protocols supported:
- Freeport: user-parameterizable telegram format for universal communication
- 3964(R) for improved transmission reliability
- Modbus RTU Master
- Modbus RTU Slave
- USS, implemented through instructions
Interface properties:
- RS 232 with auxiliary signals
- RS 422 for full-duplex connections
- RS 485 for half-duplex and multi-point connections
- Transmission rates from 300 to 115 200 bit/s
- Connection via sub D connector
Data communication via IO-Link communication modules
Up to eight IO-Link devices can be connected via the CM 8xIO-Link communication module.- IO-Link Master according to IO-Link specification V1.1
- Data transmission rates COM1 (4.8 kBd), COM2 (38.4 kBd), COM3 (230.4 kBd)
- Parameterizable diagnostics can be set for each channel
- Master backup with “IO_LINK_MASTER_8” function block
- Replacement of IO-Link devices (only for V1.1 devices)
- Supports firmware updates for IO-Link devices
- Variable address range for I/O data with up to 240 byte inputs and 240 byte outputs
Expansion limits:
-
- Max. 32 bytes of input and output data per port
- Max. 240 bytes of input and output data per module
- Port Qualifier Information (PQI)
- IO-Link port configuration with S7-PCT
- IO-Link port configuration with STEP 7 or GSD (without S7-PCT)
Configuration with SIMATIC STEP 7 Professional V12 or higher engineering software (S7-1500R/H with V15.1 or higher)
- PROFINET IO IRT interface (2-port switch), integrated in the CPU (PROFINET RT only for S7-1500R/H); for defined response times and high-precision plant behaviour.
- Communications processors for connecting to the PROFIBUS, Industrial Ethernet and PROFINET bus systems
- Communication modules for point-to-point connections.
From CPU 1515, all CPUs feature one or more additional integrated PROFINET interfaces with separate IP address, e.g. for network separation or for connecting additional PROFINET IO devices. From CPU 1516-3 PN/DP, PROFIBUS nodes can be connected via the integrated PROFIBUS interface. The CPUs without integrated PROFIBUS interface can be easily expanded via a PROFIBUS CM.
Process communication via PROFINET IO
The SIMATIC S7-1500 is connected to the PROFINET IO bus system via the integrated PROFINET interface and permits a distributed automation configuration with defined response times and high-precision plant behaviour.
The distributed I/O via PROFINET IO is treated just like a centralised I/O from the user’s perspective (same configuring, addressing, and programming).
The following can be connected as IO controllers:
- SIMATIC S7-1500
- SIMATIC S7-1200
- SIMATIC S7-300 (via CPUs with PROFINET interface or PROFINET CPs)
- SIMATIC S7-400 (via CPUs with PROFINET interface or PROFINET CPs)
- SIMATIC ET 200 (via CPUs with PROFINET interface)
The following can be connected as an I-device or device:
- SIMATIC S7-1500
- SIMATIC S7-1200 (FW 4.0 or higher)
- ET 200S IM151-8 PN/DP CPU, ET 200pro IM154-8 PN/DP CPU
- ET 200SP CPU 1510SP-1 PN, CPU 1512SP-1 PN
- SIMATIC S7-300 (via CPUs with PROFINET interface or PROFINET CPs)
- SIMATIC S7-400 (via CPUs with PROFINET interface or PROFINET CPs)
- ET 200 distributed I/O devices
- HMI devices which are operated as direct key modules
- Field devices
Process communication via PROFIBUS DP
SIMATIC S7-1500 (not S7-155R/H) is connected to the PROFIBUS DP bus system via a communications module or via CPUs with integrated PROFIBUS DP interfaces. The CPUs or communication modules with PROFIBUS DP interface enable distributed automation configuration with high speed and simple handling.
The distributed I/O via PROFIBUS DP is treated just like a centralized I/O from the user’s perspective (same configuring, addressing, and programming).
The following can be connected as masters:
- SIMATIC S7-1500 (not S7-1500R/H)
(via CPUs with PROFIBUS DP interface or PROFIBUS DP communications modules) - SIMATIC S7-300
(via CPUs with PROFIBUS DP interface or PROFIBUS DP CPs) - SIMATIC S7-400
(via CPUs with PROFIBUS DP interface or PROFIBUS DP CPs) - SIMATIC S5-115U/H, S5-135U and S5-155U/H with IM 308
- SIMATIC 505
The following can be connected as a slave or as an I-slave:
- Distributed I/O devices, e.g. ET 200
- Field devices
- SIMATIC S7-200, S7-1200, S7-300
- C7-633/P DP, C7-633 DP, C7-634/P DP, C7-634 DP, C7-626 DP
- SIMATIC S7-400 (via CP 443-5 only)
- SIMATIC S7-1500 (via CP/CM 1542-5 only)
Data communication via Ethernet
The S7-1500 can be connected to the Industrial Ethernet bus system via the integrated PROFINET interface or via a communication module.
The following can be connected:
- SIMATIC S7-1200
- SIMATIC S7-1500
- SIMATIC S7-300
- SIMATIC S7-400
- SIMATIC S5-115U/H, S5-135U, S5-155U/H
- Programming devices
- PCs, industrial PCs
- SIMATIC HMI human machine interface systems
- Numerical controls
- Robot controls
- Drive controls
- Devices of other manufacturers
Protocols supported:
- TCP/IP
- ISO-on-TCP (RFC1006)
- UDP
- SNMP
- DCP
- LLDP
- HTTP
- HTTPS
- MODBUS TCP
- OPC UA
The Industrial Ethernet CP 1543-1 offers the following additional functionalities:
- 1 Gbit interface
- IPv6 support
- Security: access protection by means of hardware identification, IP/MAC access list, firewall, VPN tunnel
- Communication with S5 systems via the ISO protocol
- FTP (client/server), email, SNMPv1/v3
Data communication via PROFIBUS
SIMATIC S7-1500 (not S7-1500R/H) can be connected to the PROFIBUS bus system via a communications module or via the CPUs with integrated PROFIBUS DP interfaces. The following can be connected:
- SIMATIC S7-1200
- SIMATIC S7-1500
- SIMATIC S7-300
- SIMATIC S7-400
- SIMATIC S5-115U/H, S5-135U, S5-155U/H
- Programming devices
- PCs, industrial PCs
- SIMATIC HMI human machine interface systems
- Numerical controls
- Robot controls
- Drive controls
- Devices of other manufacturers
Data communication via point-to-point communication modules
Powerful point-to-point connections can be implemented via the point-to-point communication modules. The following can be connected, for example:
- SIMATIC S7 and SIMATIC S5 automation systems and non-Siemens systems
- Scanners, barcode readers, identification systems
- Robot controls
- Printers
Protocols supported:
- Freeport: user-parameterizable telegram format for universal communication
- 3964(R) for improved transmission reliability
- Modbus RTU Master
- Modbus RTU Slave
- USS, implemented through instructions
Interface properties:
- RS 232 with auxiliary signals
- RS 422 for full-duplex connections
- RS 485 for half-duplex and multi-point connections
- Transmission rates from 300 to 115 200 bit/s
- Connection via sub D connector
Data communication via IO-Link communication modules
Up to eight IO-Link devices can be connected via the CM 8xIO-Link communication module.- IO-Link Master according to IO-Link specification V1.1
- Data transmission rates COM1 (4.8 kBd), COM2 (38.4 kBd), COM3 (230.4 kBd)
- Parameterizable diagnostics can be set for each channel
- Master backup with “IO_LINK_MASTER_8” function block
- Replacement of IO-Link devices (only for V1.1 devices)
- Supports firmware updates for IO-Link devices
- Variable address range for I/O data with up to 240 byte inputs and 240 byte outputs
Expansion limits:
-
- Max. 32 bytes of input and output data per port
- Max. 240 bytes of input and output data per module
- Port Qualifier Information (PQI)
- IO-Link port configuration with S7-PCT
- IO-Link port configuration with STEP 7 or GSD (without S7-PCT)
Technical specifications
General technical specifications | |
---|---|
Degree of protection | IP20 acc. to IEC 60 529
|
Ambient temperature
| |
Horizontal installation | 0…60 °C (display: at an operating temperature of typ. 50 °C, the display is switched off.)
|
Vertical installation | 0… 40 °C (display: at an operating temperature of typ. 40 °C, the display is switched off.)
|
Relative humidity | 10 %…95 %, no condensation |
Atmospheric pressure | From 1080 to 795 hPa
(corresponds to an altitude of -1000 to +2000 m) |
Insulation | |
< 50 V | 707 V DC test voltage (type test)
|
< 150 V | 2200 V DC test voltage
|
< 250 V | 2500 V DC test voltage
|
Electromagnetic compatibility
| Requirements of the EMC directive;
interference immunity according to IEC 61000-6-2 |
Pulse-shaped disturbance variables | Test according to:
Electrostatic discharge according to IEC 61000-4-2,
burst pulses according to IEC 61000-4-4,
energy single pulse (surge) according to IEC 61000-4-5,
|
Sinusoidal disturbance variables | Test according to:
HF irradiation according to IEC 61000-4-3,
HF decoupling according to IEC 61000-4-6Requirements of the EMC directive;
interference emission according to EN 61000-6-4 |
Emission of radio frequency interference | Interference emission according to 61000-6-4Interference emission of electromagnetic fields according to EN 61000-6-4
|
Mechanical stress | |
Vibrations | Testing according to EN 60068-2-6
Tested with: 5 Hz ≤ f ≤ 8.4 Hz, constant amplitude 7 mm; 9 Hz ≤ f ≤ 150 Hz, constant acceleration 2 g; duration of vibration: 10 frequency passes per axis in each direction of the 3 mutually perpendicular axes |
Shock | Testing according to EN 60068-2-27
Tested with: Half-wave: strength of shock 15 g peak value, 11 ms duration; shock direction: 3 shocks each in ± direction in each of the 3 mutually vertical axes |
Application Examples
- Security with SIMATIC-S7 controller
- Creating and using user-defined web pages on S7-1500
- Programming Guideline for S7-1200/S7-1500
- Migration of plants with SIMATIC (TIA Portal) - Controllers
- System Diagnostics with S7-1500 and TIA Portal
- Speed Control of a G120 (Startdrive) with S7-1500
- Application examples for S7-1500
Frequently Asked Questions (FAQs)
Build innovative machines faster without costly prototyping with Efficient Motion Control.
With Effective Motion Control, machine builders can easily overcome major challenges and enable faster time-to-market, increased functionality, resolve complex system requirements, and demands for safety and sustainability.
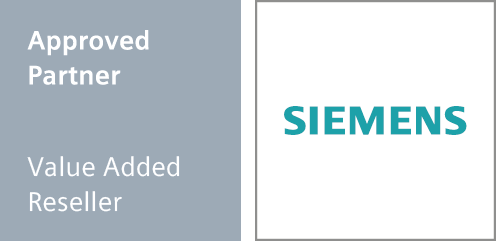
We are Siemens trusted and approved distribution partner.
As a Value Added Reseller in Siemens’ Approved Partner network, Parmley Graham are a proven supplier of a wide range of quality products in the UK and globally.
Find out more how this will benefit you or check Siemens Configurator.